Are you looking to create a custom product out of plastic? You’ll be considering injection or rotational moulding as two prominent options for manufacturing. So which one should you choose? We break down the best options for particular types of products and projects.
Recognising the right method
Here at Global Rotomoulding, we’ve undergone our fair share of custom rotational moulding projects. This includes assisting in the design phase, toolmaking, prototyping and manufacturing of a product. As veterans in the art of plastic moulding, we have a keen eye for recognising what method will produce the best results for your design. In fact, on many of our custom projects, we have outsourced injection moulding services in order to make smaller or more intricate parts of specific products.
Our collaboration with Trailers 2000 to make the TuffMate2000 Trailer required accessories that were injection moulded to complete the product within budget. Attempting to manufacture these small parts by using rotational moulding wouldn’t have made sense, as the parts themselves were not hollow; a main requirement for rotomoulding. At Global, we’re dedicated to finding the most cost-effective and efficient way to assist our clients in completing their project.
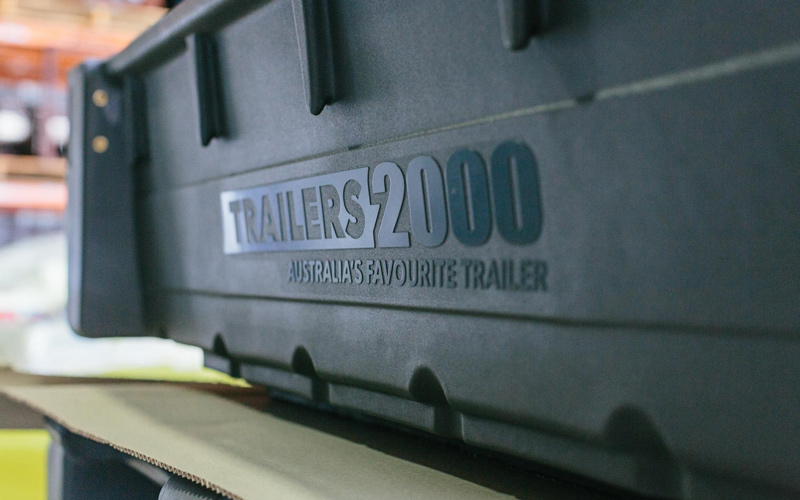
What types of products are ideal for rotational moulding?
Rotational moulding can be used to make anything that’s hollow on the inside. It’s also typically suited to large-scale products such as water tanks and livestock troughs. The fact that there are no joints in these larger products means that their structural integrity is much sturdier without adding more weight to the overall product. They’re less likely to crack or cave under pressure as a result.
A few other products that can be made using rotational moulding include:
- Containers (from a storage container to a shipping container)
- Children’s play equipment
- Pallets
- Septic Tanks
- Recycling units
- Water filtration systems
- Fuel tanks
- Medical products such as stretchers, paramedics cases and casings for medical equipment.
- Pontoons
- Kayaks
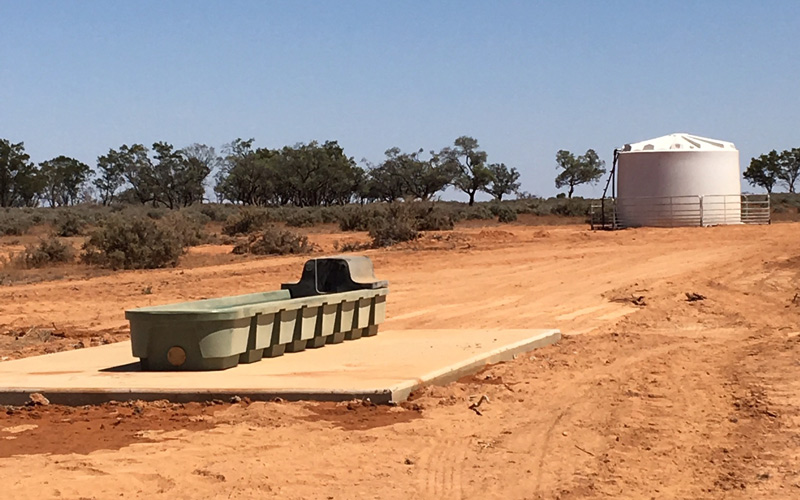
What types of products are ideal for injection moulding?
Injection moulding is best for intricate, small parts such as screws and rods. It’s often used to make children’s toys and produce large run’s of a product at a low cost.
A few other products that can be made using rotational moulding include:
- Car interiors
- Phones
- Lego
- Bottle caps
- Combs
- Musical instruments
- Medical instruments
The best of both worlds
Do you have a custom design that would benefit from both rotational and injection moulding techniques? Global can assist you in building it using these two moulding methods to ensure a sturdy, reliable and budget friendly product. Contact us today to find out more.