Moulding with plastic is a cheaper, lighter and more efficient method of manufacturing than many other materials, including steel.
However, there is a big difference between rotational and injection moulding, and we’re here to explain why our method of rotational moulding produces the best results!
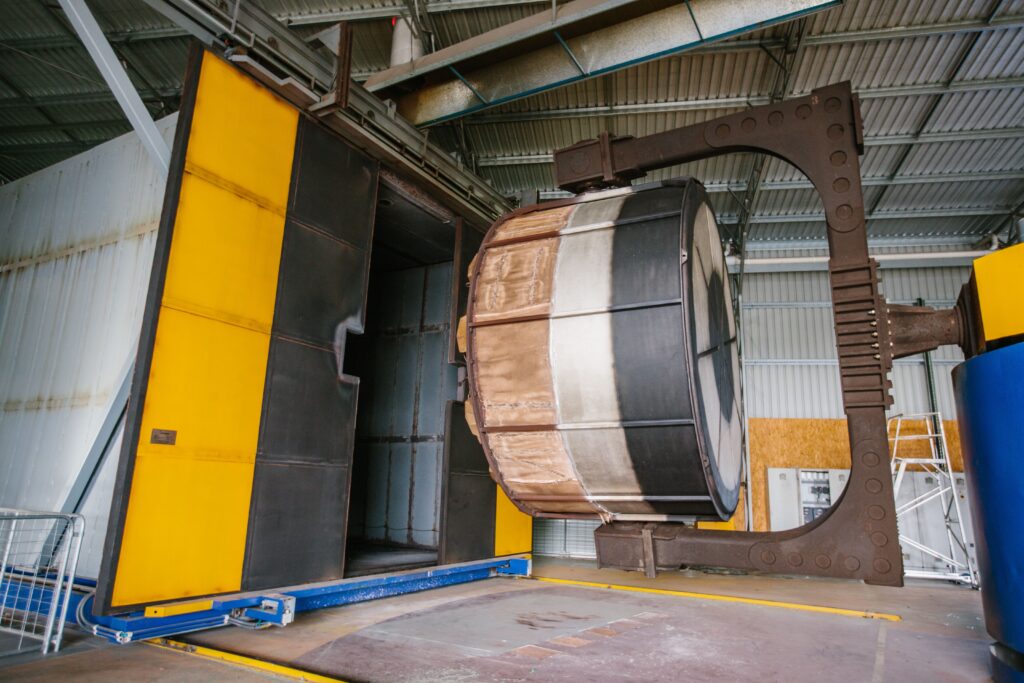
Injection Moulding
Injection moulding undergoes the process of forcing melted plastic into a mould cavity. Once the plastic is cooled, the mould can be removed from the outside. This technique is commonly used to mass produce objects such as toys and kitchen appliances. The same mould can be reused many times over.
Rotational Moulding
Rotational moulding is a process whereby powdered plastic is placed into a hollow mould. The mould is rotated on all axis within an oven, where the plastic melts to the mould and takes on its shape. It is then allowed to cool using a variety of methods, these cause it to shrink and to come away from the mould surface. Rotational moulding is used for any object that is hollow on the inside (which is way more shapes than people think), and most commonly used to make tanks and containers.
The main advantages of rotational moulding
We also work closely with injection moulders when it makes sense. For example, accessories of the recent box trailer, TuffMate 2000, were injection moulded to keep costs down.
The following is a list of benefits of rotational moulding to product design and fabrication. We’ve included a link at the end for some examples of custom products that really stretch the imagination of what can be designed out of plastic using this method.
Saving costs
The tools needed for rotational moulding are significantly cheaper. Furthermore, often multiple parts can be incorporated into the one mould, which limits part failure and labour to assemble the final product. In injection moulding, all parts need to be made separately and put together to make a hollow product.
Consistent wall thickness
The constant rotation involved in rotomoulding means that achieving consistent wall thickness is easy and possible for every product. This results in superior strength as products will not be buckling in high-stress places such as corners and joints due to thin plastic coatings. In injection moulding, the many different parts that are needed to make a product means decreased likelihood of wall consistency.
Bespoke products
Injection moulding is often used to mass produce products. Rotational moulding is more flexible and cost-effective when tailoring specific products to suit clients’ needs. Because tools are relatively inexpensive (once the design has been finalised) there’s no need to order in vast quantities to get your money’s worth.
Reduced lead times
When using injection moulding, it can take up to six months to get your product from the design to sale stage. With rotational moulding, production times are generally much quicker. Furthermore, due to the fact that rotational moulding uses cheaper tools, there is more flexibility in trialling different moulds to make sure you get exactly the product you’re looking for.
To see some examples of rotational moulding in action, visit our custom rotomoulding portfolio page.
At Global Rotomoulding we are always open to new, innovative design ideas and work closely with our clients to create products which challenge the traditional view of plastic use. Contact us today to discuss your product ideas!