Linear Economy’s
Western society has become addicted linear model of consumption
We take natural resources, we process these resources, make products and consume them for a short period of time and then dispose with the vast majority of products going to waste.
With a limited qty of natural resources we need to think smarter in the ways that we consume, recycle, reuse resources.
Circular economy
A circular economy goes back to the beginning to prevent waste and pollution from being created it challenges us to consider waste and pollution as design flaws
While recycling is undoubtedly a necessary component, we need to ensure that products and materials are designed, from the beginning, to be reused, repaired and remanufactured. It’s the consequences of decisions made at the design stage that determine around 80% of environmental impacts (source)
Circular Economy: Rethink, redesign, reduce, reuse, recycle
The circular economy has been a buzz economic model that has often been more lip service to action for a numbers of years, though in the last year or so movement, industry and customers are beginning to adopt and look at ways to extract the maximum value from them before recovering and regenerating them. Products need to be designed with durability and a long lifecycle in mind. Have a system in place that product can be repaired, reused and finally recycled to make new products. This reduces the reliance on virgin resources which minimises waste and promotes sustainability with a reduction of environmental impact.
The Ellen Macarthur foundation has a video that gives a great overview of the circular economy
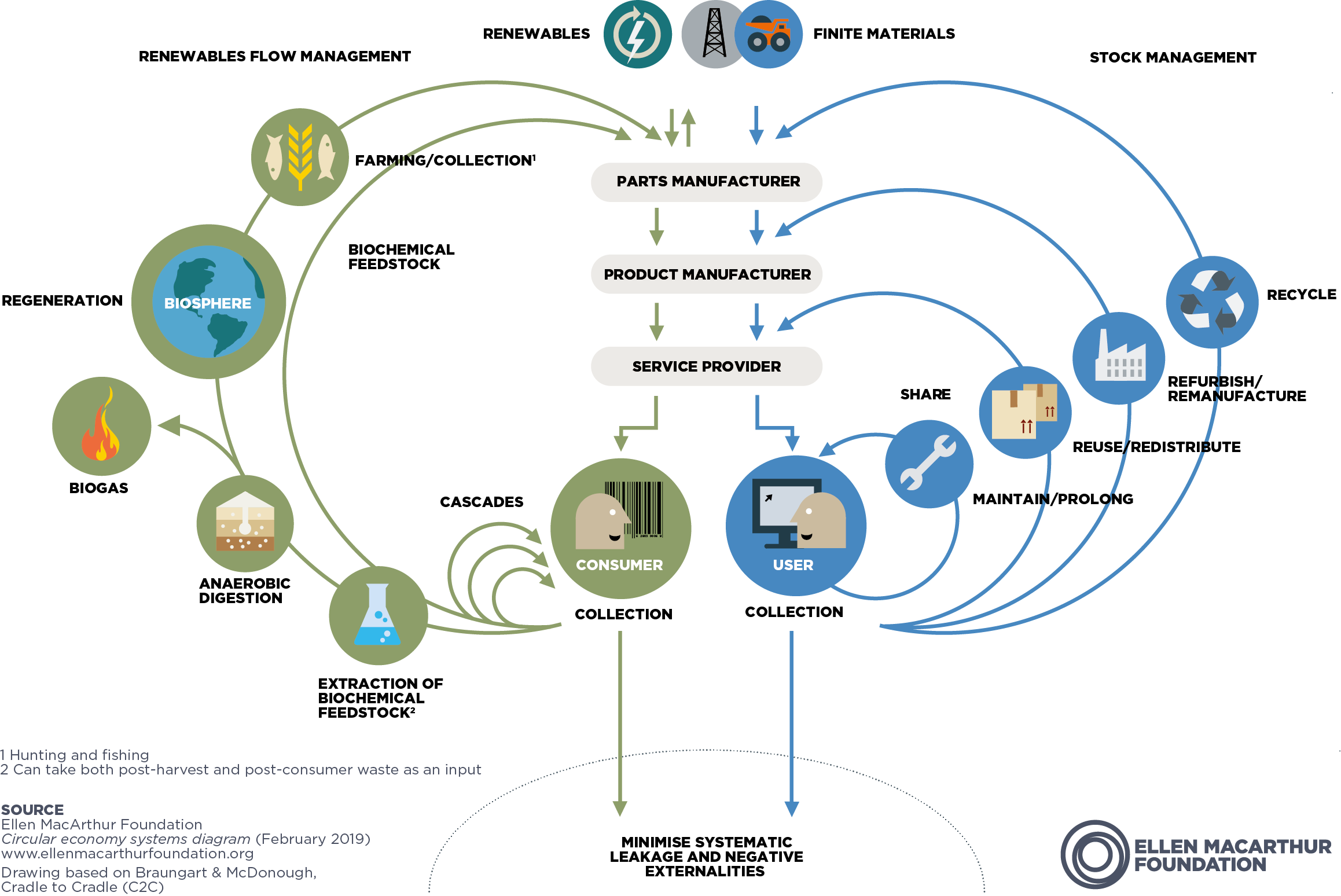
Source: Ellen Mac Arthur Foundation The Butteryfly Diagram
Global Rotomoulding believes the first step moving to a circular economy occurs at the design stage.
Creating a clear and concise design specification that takes in to account the following;
- Designing products to last for multiple years
- Ensuring the product is designed to meet the specification required to ensure full product life cycle
- Can the product be modular
- Can the product be upgraded over time with other components
- What is the most efficient way to produce the product that has the lowest energy consumption
- Can a family of products be produced which means less material required in producing multiple moulds
- For smaller products multiple products can be run in the oven at the same time to ensure energy consumption is maximised
- Finite Element Analysis FEA to ensure that products meet engineering requirements to last the test of time
When we are manufacturing we are optimising the following to reduce wastage of energy and resources
- Optimising Production schedule with QUT PhD project
- Looking to adopt solar energy
- Using energy efficient ovens saving cost in gas and electricity
- Ensuring that our run time on ovens is optimised
- Reducing our waste product by ensuring we have preventive maintenance on moulds which ensures less downgrades
- The company is working to reduce further downgrades as this is wasted energy and resources
- Improve our Dispatch and QA process
- This will help ensure we get top quality products to our customers in a timely manner which are fit for purpose.
- Looking for future advances to use more renewable energy to power our ovens.
Return of products to be recycled at end of life.
- OEM can return products via our trucking network when delivers are made to their business
- Customers can return cut up product to our manufacturing sites
- We then send this product off to be recycled. A portion of this we buy back to make new products
- Our Suppliers are working on new ways to recycle the plastic so that we can use the recycled plastic in engineered products
Global Rotomoulding will always be evolving to become more sustainable, efficient and profitable as a company. We welcome you as our customers to come with us on this journey.
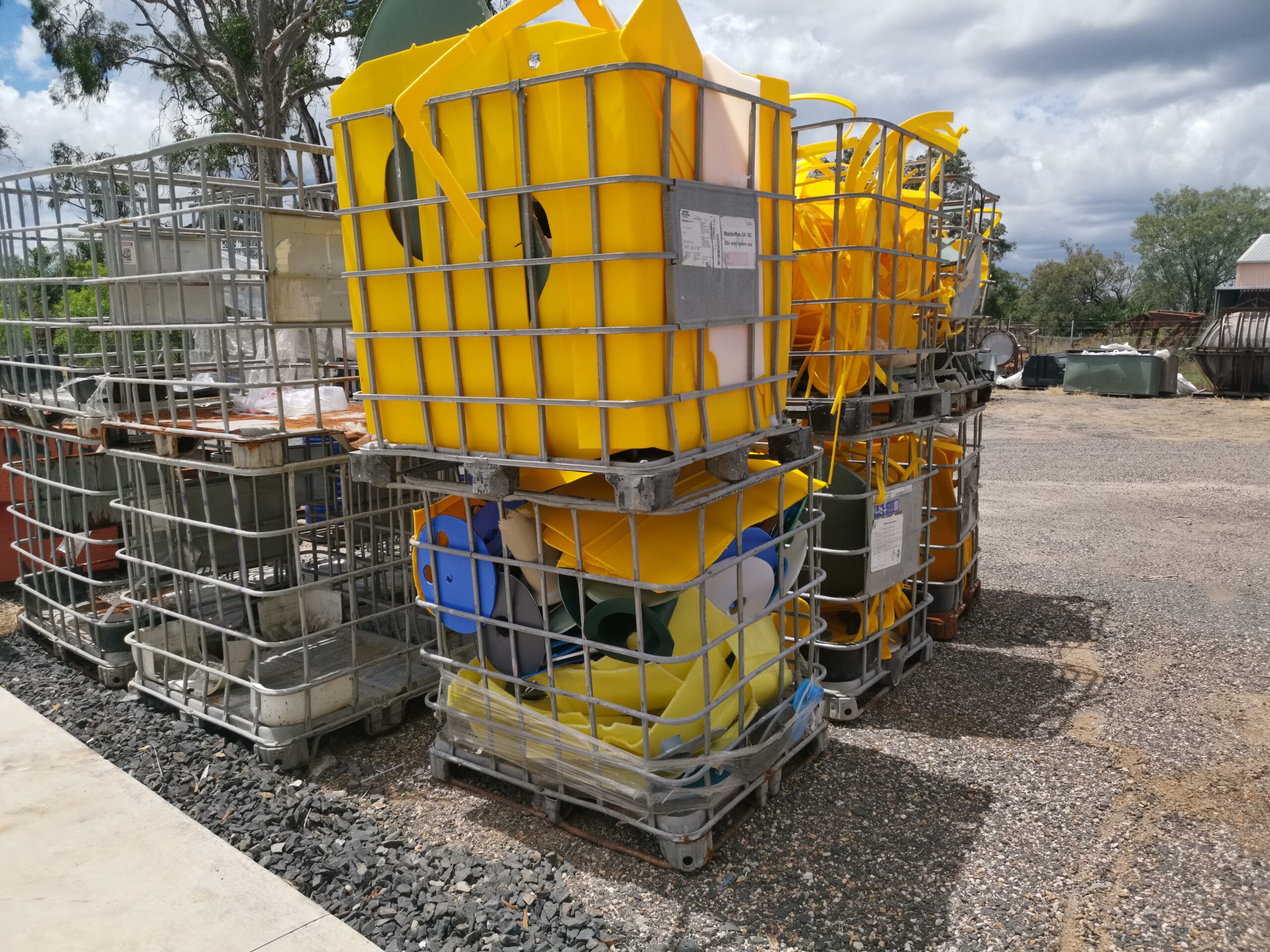
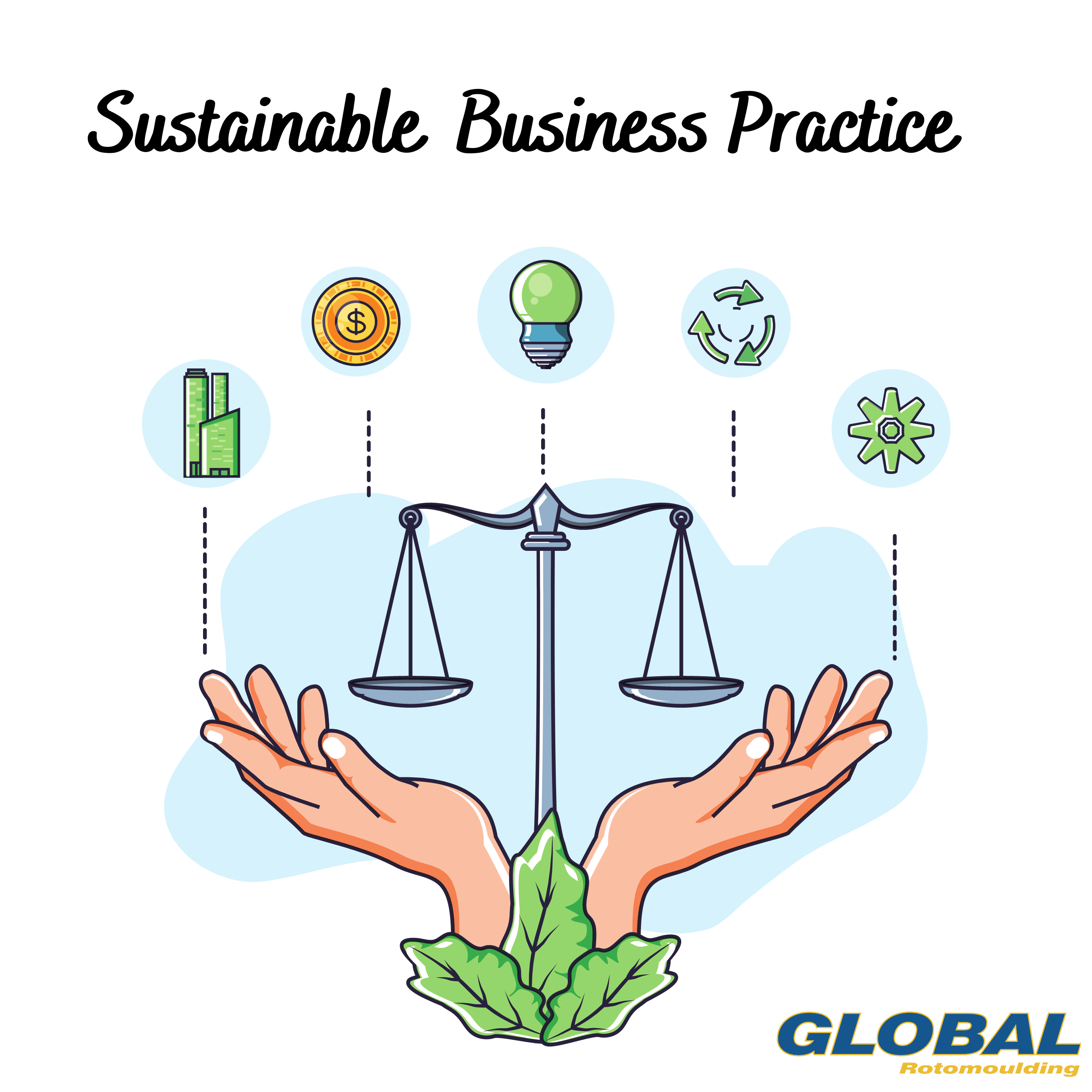