Custom Rotational Moulding
Home / Our Services / Custom Rotational Moulding
Global has successfully brought many new products to market
Examples include:
- Underground Water Retention Systems
- Children's Play Equipment
- Automotive Intakes
- Fire-fighting Water Tanks
- Fuel Tanks
- New Range of Rotomoulded Septic
- Cartage & Rainwater Tanks
The team at Global Rotomoulding began back in farming and agriculture. However over the years, we’ve worked with industrial designers from the widest range of industries. Whatever the project, we push design (and where necessary, innovation) to manufacture to our customers specification and requirements.
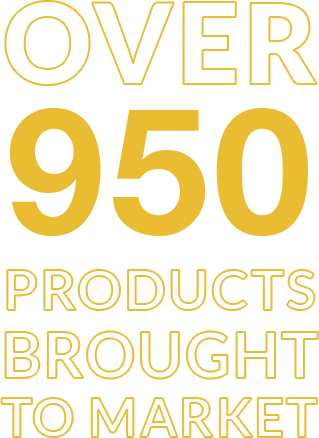
How We Help
Huge potential for plastic products
Rotomoulding has a long reputation as the best method for manufacturing polyethylene water tanks. However, recently, many manufacturers have started using the process to create plastic products for a wide range of other industries. From medical products to furniture, automotive and marine parts, agricultural tools, playgrounds, industrial garbage bins and more – the opportunities are endless!
Here are just a few of the design advantages of using rotomoulding for your next manufacturing project:
Greater durability
Consistent wall thickness
The application of molten plastic is very precise, which means you can create a consistent wall thickness around your products. This reinforces the product’s strength and hardiness, even at corners and defined angles.
Wide range of shapes
Lighter weight
Lower production costs
Resistant to rust, corrosion and UV rays
Variety of finishes, textures and colours
Safer for humans
How rotational moulding works
The process of rotational moulding (roto-moulding) is quite straightforward. First, you need a hollow mould which is filled with granulated plastic that is then heated. The mould is then slowly rotated around two axes until the softened plastic has stuck to the walls of the mould. The mould rotates throughout the heating and cooling phase to avoid sagging or deformation. At Global, we use low-density polyethene plastic as it’s stress crack resistant, UV resistant, strong and durable.
Rotational moulding, or rotomoulding for short, is a plastics manufacturing method with many design advantages. In fact, the method has become so popular in the last decade, that it’s now one of the fastest growing sectors in the plastics industry.
Our Capabilities
High capacity production with eight ovens across two sites to minimise risk.
AS/NZO ISO 9001:2016 forms the back bone of all business processes ensuring excellence and quality.
Currently Company wide DIFOT of 90% aiming for industry excellence of 95%.
Ability to design, produce and bring standards certified products to market.
Successfully working for over 30 OEM companies around Australia.
Complete product realisation services from innovative concepts throught to local manufacturing.
Robot Technology and 3D printing for prototyping and precision product trimming.
Ability to produce small to large volume orders.
Traceability and digital accountability for products from order to customer.
Expertise in producing moulds and production with complex shapes within the constraints of the polyethylene medium.
Transparency and ability to maintain high quality standards through our web QA, Production notes and production schedule.
Contact us for a free quote today
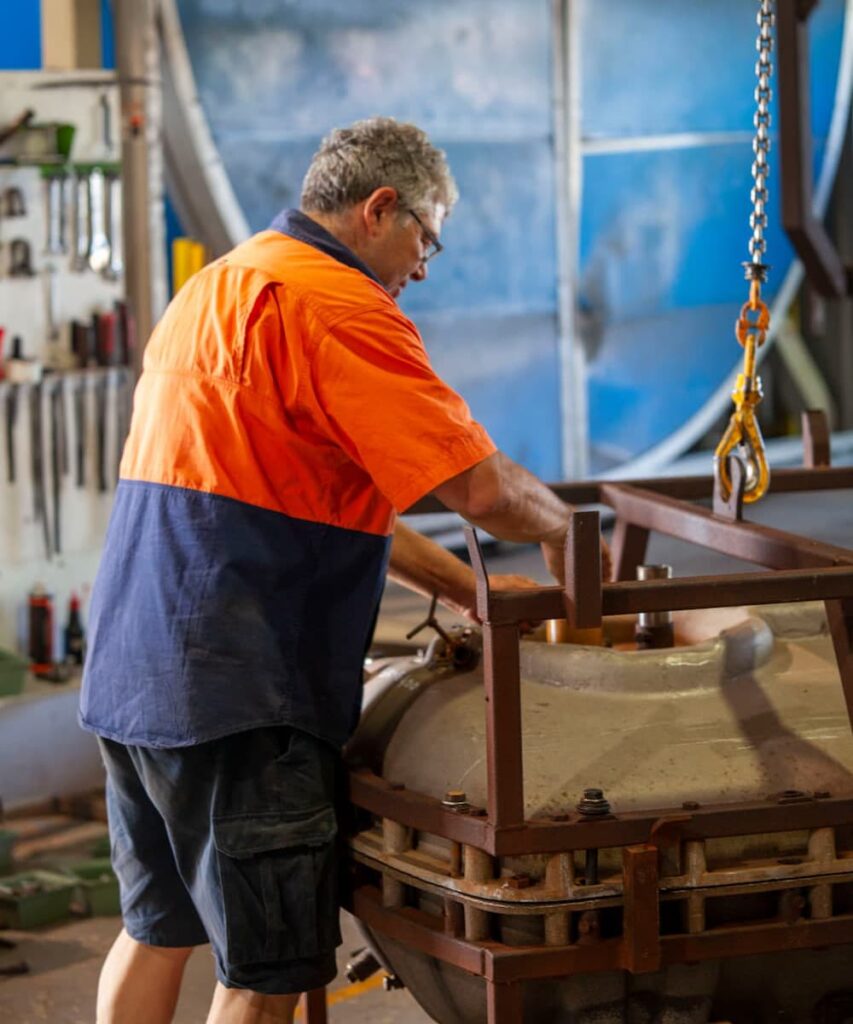