UBI Aqua Mk II Plug Adapter
Home / Case Studies / UBI Aqua Mk II Plug Adapter
Background
The UBI Aqua MKII is a secondary wastewater treatment system that relies on a series of discrete chambers (settling → aeration → disinfection) to achieve proper effluent quality. Each chamber must remain hydraulically isolated so that flow volumes, oxygen levels, and treatment chemistry stay within design parameters.
The challenge
When an internal pump fails or needs upgrading, technicians normally have to:
- Breach the tank wall, breaking the seal between chambers.
- Disconnect hard-wired electrics, requiring a licensed electrician.
- Re-seal the system and hope alignment tolerances are restored.
This process risked:
- Cross-contamination between treatment stages.
- Process upsets from unwanted mixing.
- Extended downtime and higher service costs.

The solution
Global’s team created a 3 piece, 3-D-printed plug-through wall fitting that:
- Routes the pump’s plug & lead straight through the wall of chambers with in the tank.
- Uses a silicone bead and four stainless screws to form a watertight compression seal—no gasket required.
- Allows external disconnection/reconnection of the pump, so the tank never needs to be opened and no wiring is touched.
- Installs with basic hand tools; replacement takes < 10 minutes.
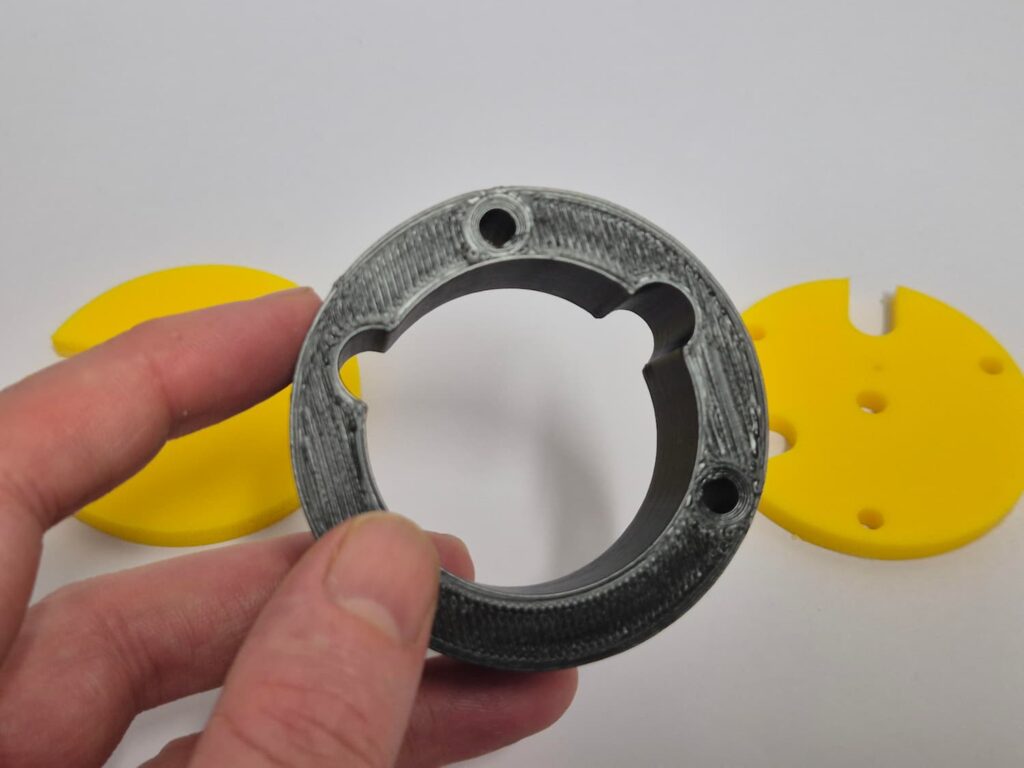
The result
- Chamber separation preserved: Treatment stages remain fully isolated, protecting performance and compliance.
- No electrician required: Field staff or service agents can swap pumps safely, cutting labour costs by ~35%.
- Shorter downtime: Average pump-change window dropped from ~2 hours to < 15 minutes.
- Scalable design: The printed fitting can be iterated quickly for future pump models or retrofits.

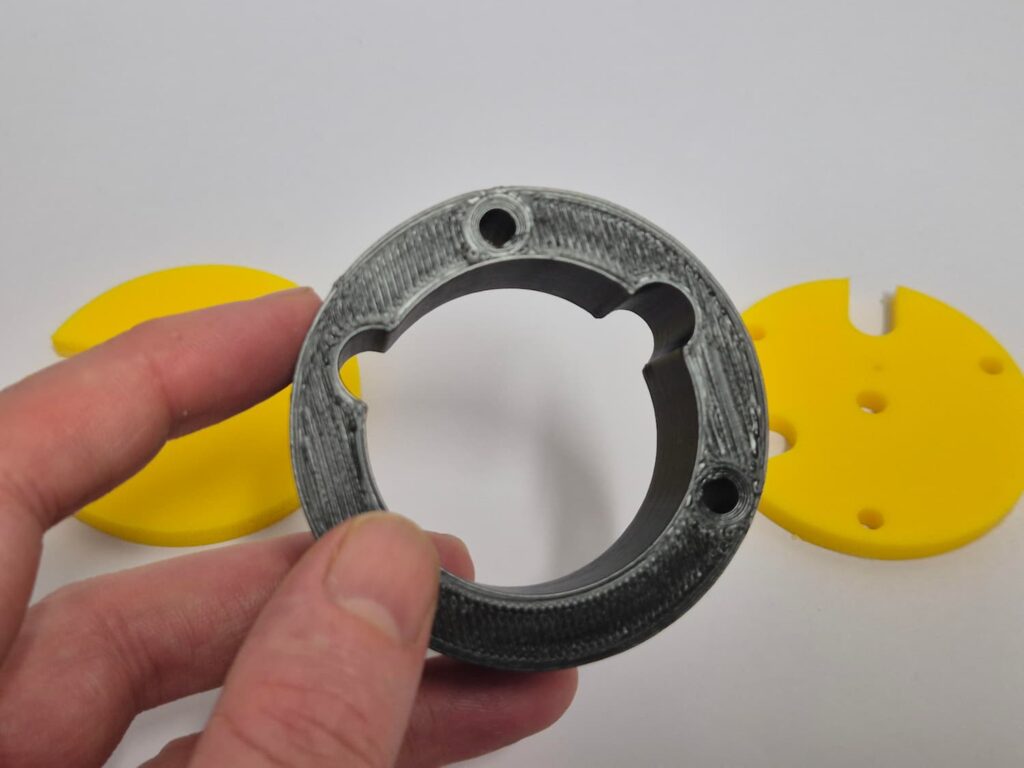
Key takeaways
- Process integrity first: By preventing cross-mixing, the fitting safeguards effluent quality and regulatory compliance.
- Rapid prototyping pays off: 3-D printing let the team refine geometry and screw boss spacing in days, not weeks.
- User-centric engineering: Removing electrical work from the task list made servicing simpler, safer, and far cheaper for customers.
Global Roto-Moulding continues to leverage additive manufacturing and practical field feedback to streamline every facet of its wastewater product line—proof that even small components can deliver outsized value when designed with the end-user in mind.
Get a free quote for your rotational moulding project
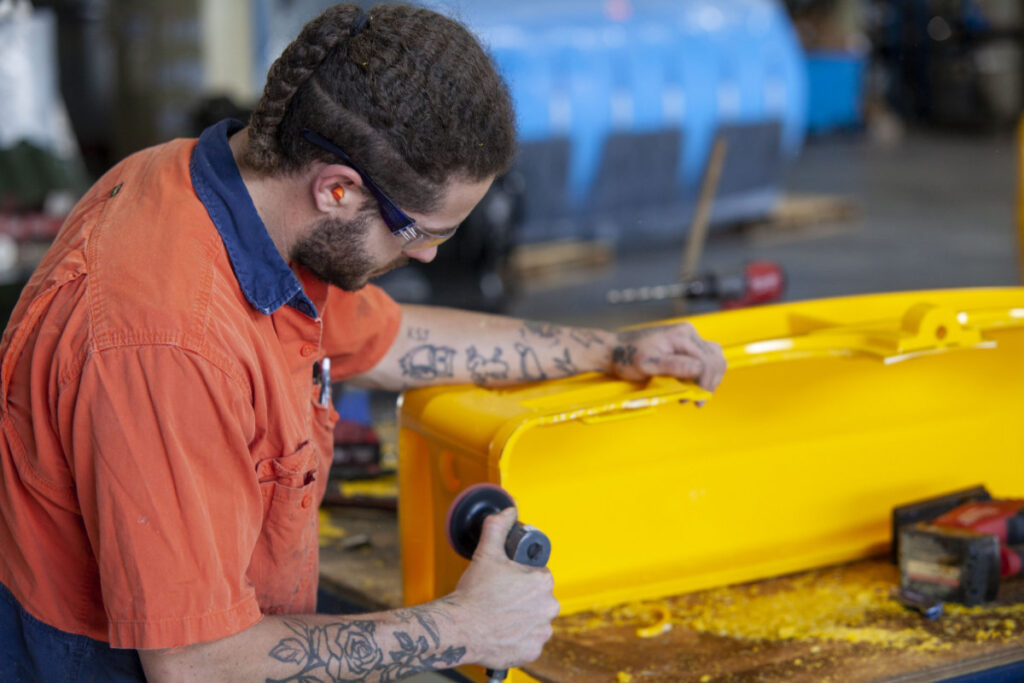